As Sacramento attempts to forge a regional economic development strategy, manufacturing is being touted as a potential breadwinner, but rebuilding the industry piecemeal could take time.
Business incentives in the Capital Region include availability of industrial space, connection to major transportation arteries and young talent available from numerous colleges.
Moreover, manufacturing jobs in California pay about one-third more than the average wage, U.S. Department of Labor figures show, and factories can house plenty of personnel.
“Typically, manufacturing companies hire twice the number of
employees per square foot (of) space as the service and retail
sectors,” says John Fleming, Yuba County’s economic development
coordinator.
And when finished products ship outside the region, new money
flows in. “Rather than recirculating money within the economy,
which is retail to a large degree and the service industry to a
significant degree, manufacturing grows the cash basis of the
local economy,” he says.
But convincing companies that Sacramento can be the next major manufacturing hub has proven difficult. The area has been shedding manufacturing jobs for years while gaining few new players.
The nine-county region hosted about 49,000 manufacturing jobs as of mid-2011, down 32 percent from the previous decade. As a portion of total regional employment, manufacturing has shrunk from 6.5 percent to 4.4 percent.
Statewide, the picture looks equally grim: 620,000 manufacturing
jobs have been lost since 2001, the California Manufacturers and
Technology Association reports.
“Some companies have gone overseas, some have shut down,” says spokesman Gino DiCaro. “When a lot of these companies need to scale up, they are scaling up elsewhere.”
Nationwide, 40.2 production plants exist for every million residents. In California, there are 4.8 plants per million residents, data from Site Selection magazine shows.
“California is getting slaughtered for new investment,” DiCaro says. “It’s just not happening.”
Despite these challenges, the Capital Region has scored a few wins in the past year:
• Nippon Shokken U.S.A. Inc., a food seasoning company, bought 10 acres in West Sacramento for its U.S. headquarters, research and development labs and plant. The three-pronged operation should employ about 100 people.
• Another Japanese company, Mori Seiki Co., started building in Davis its first U.S. factory for making precision machine tools, adding an estimated 100 to 150 jobs.
• Siemens AG won a $466 million contract to build 70 electric locomotives for Amtrak. They are expected to be built at the South Sacramento plant that has been turning out light-rail cars since the 1980s.
• Telefunken Semiconductors America bought the old NEC Corp. microchip factory in Roseville and is making upgrades to increase production.
What tips the scales in Sacramento’s favor?
“In our search for a plant, we were working for a couple of things. First of all, we wanted a collaborative local government that would help us in terms of hiring and generally making the process simplified,” says Shilpa Sankaran, co-founder and vice president of marketing for Zeta Communities, which builds about 500 modular homes a year at a 91,000-square-foot plant in McClellan Park.
When the San Francisco company started scouting sites, it looked at Oakland, San Francisco, Pittsburg and other Northern California locales. In the Capital Region, it was courted immediately by the Sacramento Area Commerce and Trade Organization and the Sacramento Employment and Training Agency. Other metro areas have similar organizations but don’t show as much initiative, Sankaran says.
“More importantly right now is that there are so many other manufacturers in the area who are our partners and suppliers,” she says. About 40 percent of the company’s vendors are nearby. Its paint supplier is at McClellan Park.
That’s as good a description as any of the “cluster” strategy being implemented by the Next Economy project, a collaborative effort by Valley Vision, the Sacramento Metro Chamber, SACTO and the Sacramento Regional Technology Alliance to create a regional economic development strategy. The idea is that recruiting should include all the suppliers and support businesses that keep manufacturers humming.
Logistically, Sacramento is in a sweet spot for serving the West Coast market that Zeta caters to and for Magnum Towers Inc., a Sacramento company making towers for broadcasting and railroads since 1976. The company has recently branched out into cell phone towers and test towers for the wind power industry and is landing business as far off as American Samoa, Trinidad and Africa.
Texas might be a better location as far as being close to major steel suppliers, but Sacramento has a logistical advantage for international shipping and serving the West Coast, says Marketing Director Brandon Naffin.
“We do very well with manufacturing in terms of recruiting and being able to close the deal,” says SACTO president and chief executive Barbara Hayes. In addition to the factors cited by Magnum and Zeta, Hayes notes the relatively low-cost power from the Sacramento Municipal Utility District and Roseville Electric.
“It’s not only the cost, but they look very closely at outages and redundancy,” Hayes says of manufacturing prospects.
It is nonetheless difficult for many companies to swallow the
bitter pill of Sacramento’s location within one of the most
expensive, litigious and regulated states in the nation.
California is one of just three states that tax the purchase of manufacturing equipment. The remaining 47 states either don’t tax, or they provide credits or exemptions. California stopped providing that relief in 2003. Manufacturers also complain about the state’s rigorous environmental laws, which hinder factory construction. Moreover, lawmakers regularly turn to fees to solve state budgetary demands, adding uncertainty to business costs.
“You need predictable costs,” DiCaro says. “You can’t predict what’s going to happen from year to year. There was a pretty universal acknowledgement last year among the legislators that we’ve got to make our regulatory programs more cost effective.”
California also has rigid rules about required breaks, eight-hour workdays and overtime, Hayes notes, making the labor force a big sticking point for many manufacturers.
“The big complaint I hear from manufacturers is, ‘Send me someone who is willing to learn, who shows up on time, who is motivated, who wants to grow?”
John Fleming, economic development coordinator, Yuba County
Some small companies routinely network with surrounding colleges to recruit talent. When Magnum Towers needs an extra welder, it just calls a local community college professor for leads on the best students. Zeta also taps into the community college network to find fresh talent. Additionally, the company needs people from the construction trades, and Sacramento has a surplus.
But on a broader scale, labor is a tougher nut to crack.
“We’ve got a high unemployment rate, but we also have a career technical education problem,” says DiCaro of the manufacturers association. “Our high schools are trying to get all of their students into a four-year university.”
Companies can’t do much with a student who lacks hands-on skills and can’t read a gauge properly, he says.
“I call it a lost generation,” says Bill Browne, director of
client services for manufacturing consultant Manex Inc. in San
Ramon. He says a lack of focus on career tech is damaging the
workforce statewide.
“There are little pockets of things going on, but it is not like
there is a concerted effort to push these skill sets,” he says.
“If stuff does start to come back, there is a question of who is
going to build it.”
His view was echoed by Tom Kandris, owner of corrugated box
manufacturer PackageOne Inc.
“Manufacturing is slipping away from the U.S., so the mindsets of
70 or 80 percent of the people are in services. I won’t say they
are looking for an easier work path, but it is harder to find
people who are not afraid of hard work and also have basic
mathematic and language skills.”
Fleming hears the same thing in Yuba County.
“The big complaint I hear from manufacturers is, ‘Send me someone who is willing to learn, who shows up on time, who is motivated, who wants to grow.’ Those are of greater concern in today’s environment,” he says.
But willingness and motivation are measured on a different scale in different countries. In January, The New York Times detailed Apple Inc.’s shift in manufacturing from the United States to Asia. It described Chinese factory workers living in on-site dormitories, working 12-hour shifts.
The article described a government willing to heavily subsidize
industry, to the point where a Chinese glass manufacturer showed
Apple execs a newly built wing on the factory, “in case you give
us the contract.”
Big manufacturers are prize catches, but they can just as easily
take jobs away on short notice. Apple once had a factory in Elk
Grove, but it was converted to a call center in 2004. Another
computer company, Packard Bell, once had nearly 5,000 workers at
the former Sacramento Army Depot. That was in 1995; five years
later, the company had become Packard Bell NEC and shuttered
production entirely.
Given the unpredictable direction of major manufacturers, Hayes of SACTO says she would prefer to diversify regional talent to fend off another industry bubble.
“I’d rather have my eggs in a lot of different baskets,” she says.
But a question arises as to how small companies can be and still benefit the local economy. Zeta has 60 or so factory workers and intends to expand to 80. Around Sacramento, that’s big, since 78 percent of manufacturers in the metro area have 20 or fewer employees, U.S. Census figures show. Sixty-three percent have 10 or fewer, which is Magnum Tower’s size.
“If you can get the big hits, there are economies of scale, but I don’t know that you are going to get the big guys coming out there,” Brown says. Building the job base by 10 to 30 jobs at a time is slow going, he adds, “but if that’s where we have to go, we have to somehow make it a viable place for some of these companies to set up shop.”
Recommended For You
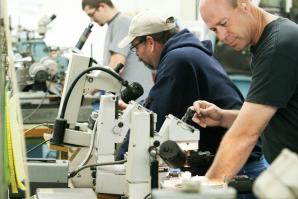
Right to Assembly
Growing manufacturing jobs in Placer County
If a local economy is thriving and healthy, it may have the manufacturing industry to thank. If things aren’t so good, it’s probably because manufacturing jobs are leaving.
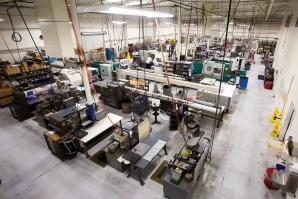
Brain Power
Research and development is the foundation for regional manufacturing growth
Like an oil derrick with arms, the school-bus-yellow robot is the center of attraction in an otherwise colorless room dominated by metal castings and concrete floors. Moving like a mime on a street corner, the robot picks up a metal casting, holds it to a computer-run camera and then places the part and the fixture that holds it on a machine for tooling.