The cost of lumber, steel, asphalt and other construction materials has been on a wild ride since the early part of this decade, but don’t be fooled by the relatively placid prices in 2009. Industry players say it’s likely just a brief respite before the roller coaster starts climbing again.
“We’re going to see relatively little movement for the rest of the year,” says Ken Simonson, chief economist for The Associated General Contractors of America, based in Arlington, Va. “I’ve been calling this a limited-time sale.”
But once the holidays come around, look out.
“By November or December 2009, I think the fire-sale numbers that we’re seeing now will be gone,” says Ron Brown, president of Brown Construction Inc. of West Sacramento.
It may be a fire sale compared to the startling heights reached by construction materials since the turn of the century, but the prices for most materials were still higher in May than they were at the end of 2003 — sharply higher, in some cases. Costs have been driven up by factors as varied as the domestic construction boom, development in China and India, labor unrest in Chile and a dramatic spike in the price of crude oil. Although economic woes have eased demand for construction materials in the near term, many of those forces are still in play.
“By next year, we could be back to the volatility,” Simonson says.
For much of the past generation, construction materials prices behaved a lot like prices in general, with single-digit percentage increases and the occasional decline. That changed in 2004. That year gypsum wallboard jumped 20 percent, according to the U.S. Bureau of Labor Statistics Producer Price Index. No. 2 diesel fuel, important for running heavy equipment and transporting bulk materials to a construction site, jumped nearly 38 percent while steel mill product prices rose almost 49 percent.
This was no isolated spike. Driven by enormous demand from domestic builders and the modernization of China as it prepared for the 2008 Olympic Games in Beijing, the price of construction materials kept climbing through early 2008 and peaked that summer.
“In this economy, virtually all products are under pressure.”
Dave Lucchetti, president, Pacific Coast Building Products Inc.
From December 2003 through May 2009, the Consumer Price Index — which tracks inflation based on the price paid by urban consumers for a typical selection of goods and services — rose about 16 percent. The Producer Price Index for “inputs to construction” — which leaves out storage, transportation and other factors that might drive up the cost of a finished building — increased 31 percent over the same five and a half years.
By mid-2008, the global economic slowdown had hit. Home building was already down to a comparative trickle, and other types of construction trailed off too. From May 2008 to May 2009, the price of many materials was down, and in some cases down a lot. Lumber and plywood fell 13.8 percent, aluminum mill shapes were down 23.7 percent, and steel mill products were down almost 40 percent. The plummeting price of oil knocked diesel fuel down 58 percent in a year.
But it’s still a global market for materials, and a complicated one. Producers have shut down plants or scaled back operations. Suppliers have adjusted inventories or set hedges against rapid price changes. Governments around the world are targeting stimulus efforts to construction, setting wheels in motion for future demand.
The result this summer is a market in flux, with some materials prices staying steady, some rising and some still ebbing. “We’ve had a substantial drop in the price of diesel fuel, asphalt, steel and copper,” Simonson says. “We did see a fairly sharp bounce off the floor for diesel and copper.”
Copper is particularly sensitive to price, he says, because it’s mined in just a few places. That means a strike or earthquake in Chile or civic unrest in the Democratic Republic of the Congo can move U.S. prices.
The complex fluctuations have applied extra pressure to local players. “For most of our product line, the materials costs are fairly stable,” says Rick Wylie, president of McClellan-based Beutler Corp, a heating, ventilation and air specialist. The exceptions are steel and copper. “They’ve been on quite a roller coaster.”
Beutler and others in the industry tried to smooth out the peaks and valleys through hedging, but some got caught leaning the wrong way when the trend shifted to falling prices. “We’re still paying for our copper based on a price that’s about a year and a half old,” Wylie says. Because of the slowdown in home construction, “we’re working through that inventory more slowly.”
“If we happen to be working on a project that uses a lot of lumber, we track that and try to let the customer know (about price trends) weekly.”
Ron Brown, president, Brown Construction Inc.
The result has been pressure on margins. “My end customer, the builder, has had to lower his prices, and he’s had to go upstream to us,” he says. “It’s been a painful process. We’ve had to lower our prices significantly, and there hasn’t been much help on the materials costs.”
“We need an increase (in prices), but we haven’t been able to get it,” says Nevin Holly, center manager for Cen-Cal Wallboard Supply in West Sacramento, a division of national player L & W Supply. With construction down, demand is soft and there’s still too much supply nationally, even with some manufacturers closing plants or reducing production.
Cen-Cal still is seeing some demand from projects such as the expansion at Thunder Valley Casino and the new Sacramento International Airport terminal, but delays and postponements at major retail centers in the area have hurt.
“In this economy, virtually all products are under pressure,” says Dave Lucchetti, president of Pacific Coast Building Products Inc. in Rancho Cordova.
And the pressure is at levels not seen in decades, he says. In a good year, California sees 150,000 to 200,000 housing starts, he says, and even in the slump of the early 1990s, the numbers topped 80,000. “We’re talking 30,000 to 40,000 housing starts this year.”
Brown Construction had to educate customers about the volatility of materials prices when they were soaring and keep it up as they fell. “Now things have sort of settled down,” Brown says. Producers have cut capacity, and inventories are down, so some materials are starting to increase in price though demand is still slack.
That could change quickly, though, depending on the economy and related factors.
Last year China announced a massive infrastructure stimulus worth the equivalent of $585 billion for construction, Simonson says. That’s a hefty chunk of government-backed demand. The U.S. stimulus package includes about $135 billion for construction, the contractor association calculates.
It expects the construction producer price index to stay roughly flat or decline slightly through 2009 then return to increases of 6 to 8 percent with occasional spikes.
For now, lower prices for some materials might create opportunities.
“If we happen to be working on a project that uses a lot of lumber, we track that and try to let the customer know (about price trends) weekly,” Brown says.
A dip in prices might mean a savings of millions if the client moves faster than the original project schedule. “We have had instances where the difference is enough to make the project go or not go.”
Recommended For You
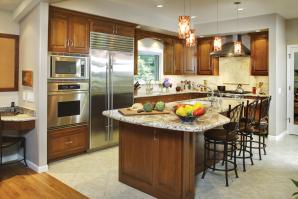
Construction Reconfigured
Baby boomers drive growth as housing market rebounds
After the worst recession in recent history crippled new home construction and forced almost one-fifth of homebuilders belly up, the future is finally looking brighter for contractors in 2013.
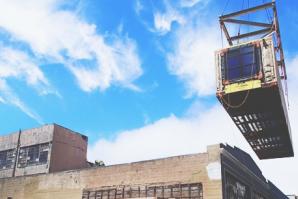
Putting the Fab in Pre-Fab
Modular construction cuts construction and energy costs
The final stages of construction at a trend-setting apartment project in San Francisco’s SoMa neighborhood, known by its address at 38 Harriett St., largely resembled a life-sized game of Tetris.