As Bay Area businesses begin to regain their financial footing, the city of Tracy is aiming to capitalize on a growing need for industrial space in an accessible, affordable zip code.
Tracy’s sales pitch should sound familiar to Sacramentans: easy access to several major transportation arteries — in this case, Interstates 5, 205 and 280 — rail connectivity and proximity to seaports.
Tracy doesn’t have a port, but the city sits just 20 miles from the Port of Stockton — the same distance from Roseville to the Port of Sacramento. And imports and exports Stockton can’t manage, the Port of Oakland can; it is just over the Altamont Pass, giving Tracy easy access to its ships and the Bay Area’s 7 million people.
Prologis Inc., a global industrial landlord, owns more than 4 million square feet of space in Tracy. Speaking at Tracy’s State of the City event earlier this year, Prologis chairman and co-CEO Hamid Moghadam said he would be surprised if his company doesn’t double its holdings there in the next three to five years, investing $300 million to $400 million and creating a potential 4,000 jobs.
“The Bay Area is a hub for global trade. The problem is, there is very little real estate in the Bay Area to support that activity,” Moghadam says. “There is very little affordable housing. There is, frankly, very little quality labor to support this kind of economic development. Tracy offers all those things in one location.”
Silicon Valley might have fit the bill 30 years ago, but not with
today’s housing costs.
Proximity to the Bay Area is key because California’s economy has
been returning to health much faster along the coast than inland.
Silicon Valley property values are on the rise again, and the
unemployment rate had dropped to 8.4 percent as of late spring.
As that part of the state’s economy heats up, Tracy is close enough to latch on. The Stockton/Tracy area still struggled with an industrial vacancy rate of 14.2 percent early this year, as measured by Colliers International, down from 19.2 percent at the end of 2010.
When people talk about Tracy’s industrial space, the subject narrows quickly to distribution, often centered on food. Safeway Inc., Costco Wholesale Corp., H.J. Heinz Co. and Crate & Barrel all have Tracy distribution centers.
Safeway’s operation is huge: 2.2 million square feet and 1,700 employees. From Tracy, trucks rack up about 24 million miles a year supplying 252 stores from Monterey north to the Oregon border, and east as far as Hawthorne, Nev. The Tracy warehouse also ships about 100 to 120 containers a week to stores in Hawaii.
A few decades ago, Safeway’s distribution was based out of Richmond. It had dry goods in one location, refrigerated food in another and health and beauty products in a third, says Jack Mixey, distribution director for Northern California.
But in 1988 a spectacular fire burned its dry grocery warehouse to the ground. Safeway decided to consolidate and in 1992 picked a campus in Tracy.
“The majority of our stores are on both sides of the bay and up into the peninsula,” Mixey says. Supply plants are in the Bay Area as well. Putting the distribution center in a place like Sacramento would only put extra miles on the trucks.
That doesn’t mean Tracy always comes up the winner. Logistics can get tricky, and finding the right spot means aligning a perfect combination of variables, including distance from markets and suppliers, cost and amount of space, and modes of transportation. Goods usually go out the door by truck, but they might come in by rail or ship.
“It’s one of those spreadsheets you would never want to put together yourself,” says Matt Cologna, senior director at commercial real estate brokerage Cushman & Wakefield Inc. in Sacramento. Companies also consider California emissions regulations and whether it’s worth picking a spot where trucks can refuel cheaper on the other side of the state line.
“The costs of consumer goods are very directly related to the cost of the movement of those goods,” Cologna says, recalling a client looking for the best distribution option in the west. Cologna plotted the annual miles the trucks would have to cover from various cities.
“When you looked at the average miles traveled, Sacramento and Stockton, for this particular company, were within one mile traveled. But when you looked at the inbound freight costs, that’s where the spike was,” he says.
Operating the same amount of space for a year could cost $100,000
to $1 million depending upon location in Tracy, Sacramento,
Stockton or Modesto.
There’s still one more choice factor that’s made Tracy more attractive: a city government that’s gotten its act together.
Another client figured it would be cheaper to move goods from San Joaquin County but learned it could obtain empty shipping containers from a Woodland company importing from China, eliminating most of the costs of having containers delivered.
A third client found the inbound freight costs from Oakland to
Woodland or Tracy were comparable, but Woodland space was
cheaper.
That deal went to Woodland, but if drive time is the key factor, Tracy may get the nod.
“Let’s say the territory of where a truck was going included Southern California up through Reno. I’m going to be better off putting myself in Tracy because I will be able to hit the drive times to Southern California without having to give my driver a break,” Cologna says.
Sacramento would offer a closer start to Reno, but Reno is a smaller market. And the Bay Area is an easier shot over the Altamont Pass than down Interstate 80.
Amount of space also is, of course, a factor.
Owens & Minor Inc., which distributes medical supplies to hospitals, consolidated its Livermore and Lathrop operations in Tracy. It needed 261,000 square feet and minimal disruption to employees.
“It comes down to availability of real estate and the buildings that would fit what we needed and the time we needed it,” says Wayne Dishman, director of real estate.
Owens & Minor serves all of Northern California from Tracy, but a lot of its customers are in the Bay Area. The farther from the Bay Area, the cheaper the space, Dishman says. But venture too far and the extra miles can wipe out the savings.
“There weren’t a lot of choices. A handful, not a bucketful,” Dishman says.
In the Sacramento area, a 100,000-square-foot tenant is considered “huge,” according to Cologna, who closes about a dozen such deals in an average year. Meanwhile in the Stockton area, he says 100,000 square feet is the typical starting point, and deals there can top 1 million square feet. The county is running out of inventory for spaces that large.
Basically, Tracy and the rest of San Joaquin County get the regional distribution centers, and Sacramento gets the local distribution centers, he says.
There’s still one more choice factor that’s made Tracy more attractive: a city government that’s gotten its act together.
“Tracy was known as a really difficult place to do business,” says City Manager Leon Churchill. “We had to rethink our planning and permitting process.”
Much of that has been automated now, many building-related fees have been cut by 20 percent to 40 percent, the city introduced incentive and loan packages and the staff was ordered to adjust its attitude. The city will expedite applications for an additional fee, and Andrew Malik, Tracy’s development services director, goes to trade shows throughout the state to drum up interest.
Not all parties get what they want, Churchill says, but they know what they are getting and when it will be delivered. The city also is making more industrial land available by annexing about 6,600 acres.
“I’m glad they admitted they had a bad reputation,” Cologna says. “They had, in the heyday, some of the highest development fees for industrial. It would have been maybe $7 or $8 a square foot in Stockton, and in Tracy it could have been $12 to $14. A pretty big spread when you are talking about a half-million-square-foot building.”
There’s strategy behind the push for more industrial tenants, Churchill says. If a company can distribute from Tracy, they could manufacture there too. About a quarter of the workers at Lawrence Livermore National Laboratory live in the Tracy area, so maybe Silicon Valley firms will see Tracy as a place to move an idea from invention to production, all within driving distance of headquarters.
“Also, we have conversations from time to time with companies in the alternative energy industry and other high-tech concerns that want to scale,” Churchill says.
If Tracy gets lazy, it could get stuck as a distribution hub. That’s not terrible, he says; distribution means jobs. But if Tracy remains vigilant, it might be able to fill that industrial space with a wider variety of tenants.
“It fits into larger land-use decisions. We’ve got to move away from being a commuter town and a bedroom community and become a full-service community,” Churchill says. “It’s making sure we are pushing up the supply chain.”
Did you know?
It’s not all about distribution. While transportation and distribution comprise a large portion of Tracy’s industrial tenants, they don’t have the entire market to themselves. A diverse group of manufacturers also have carved out some space. American Custom Meats opened a 65,000-square-foot “protein-processing facility” last year, employing about 30 people. Owens-Illinois Inc. has a glass plant on the west side of town, and Ro-Lab American Rubber Co. Inc. has its 65,000-square-foot headquarters and factory to the southeast. City manager Leon Churchill says he would like to see more names on the list. Residential development has proved troublesome as an economic development strategy for Tracy, he says. Adding more manufacturing to the transportation and logistics base could spur development from a different direction. “There is some theory behind that. The job creation will lead to housing demand, which will lead to retail development,” he says.
For more information about Ken James: www.kjamesimages.com
Recommended For You
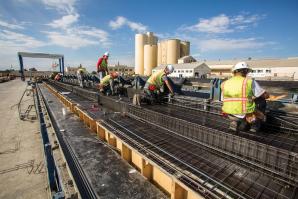
Home Field Advantage
Clark Pacific's winning stadium bid scores big for the region
The day Clark Pacific won the bid to provide the concrete components for the 49ers’ new football stadium in Santa Clara was a day for much celebration. It was a $20 million award. It meant new jobs. It meant an economic boost for the region.